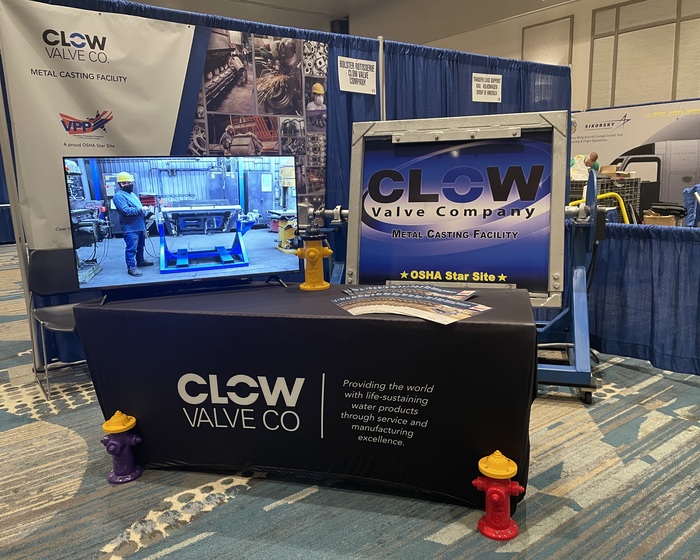
At Clow Valve, just the potential for an injury is enough to take a second look at improving work processes.
Among Pattern Maker Rick Thompson's tasks, there was one process giving him pause, the task of replacing bushings in bolsters. In the process of casting valves and hydrants, patterns are required. These patterns require a bolster to carry them in and out of the machine. Due to wear created by sand and thousands of cycles daily, bushings need replaced on bolsters frequently to ensure quality products are cast. There were no previous injuries related to the old process, however there was a significant ergonomic risk from pushing and pulling with the potential of being crushed by the 1700-lb bolster.
Thompson knew flagging a hazard is not only encouraged but also a welcome opportunity for improvement at the company. Together a team including MCF Safety Manager Tony Ingle, Nurse Administrator Mitzi Fisch, Health and Safety Manager Joe Young, Project Engineer Jake Van Polen, Business Intelligence Manager Chris Moody, Production Supervisor Jeff Beuthein, and Pattern Maker Rick Thompson, worked to develop a solution.
"Clow Valve has a culture of stepping up and ensuring all team members are able to go home safely," Ingle said. "Without being aware of this issue, we don't have an opportunity to address it. It just comes to stepping up – when we see something, we say something. We can then get the right people involved to address and correct it."
In just three weeks, the team had its first working version of the Bolster Rotisserie. The innovative design eliminated the manual lifting and turning of bolsters and reduced the amount of force needed to perform the job. After refining, it was clear the design was a natural fit for McWane's annual Ergo Cup Competition, an event that challenges team members to present ergonomic-related projects implemented to reduce injuries while improving workplace efficiency.
"It is awesome that we are preventing an injury from happening instead of being reactive," Fisch said. "We are being proactive. Anytime we can prevent an injury, that is a win in my book."
But this proactive safety mindset is not a first for Clow Valve.
In 2015, the company won the McWane Ergo Cup with its Brass Hydrant Torque Table, a custom station that eliminated the intensive manual work inserting brass inlets into wet barrel hydrants, reducing upper body stress to produce hydrants. In 2018, the Machine Shop won the McWane Ergo Cup with its Pipe Flange Painting Device, a device that eliminated the risk associated hand-painting the threaded section of ductile pipe where a flange was installed. In 2019, the Metal Casting Facility won the award again for the Brass Pattern Rotisserie. The rotisserie was a custom-built device made to manipulate brass patterns for pattern work. A fourth win in the last six years represents an ongoing culture of responsibility.
"The drive to be good was not good enough, that we wanted to be great,” Van Polen said. “As a team, we wanted to reduce the risk altogether."
After winning the McWane Ergo Cup, the team's work landed a spot competing at the National Ergo Cup at the National Applied Ergonomics Conference alongside teams from Tesla, PPG Aerospace, Nucor Steel, Volkswagen Group of America and more. While the team didn’t take home a first-place win, they received positive feedback from the judges and learned best practices from others in the industry. Ultimately, the project is a testament to Clow Valve's ability to nurture communication and teamwork at all levels.
"This is a project that's easy to have a lot of pride in because it started with hazard recognition, which is sometimes the hard part and sometimes the easy part. But then it's the communication up to management noting we've got a problem followed by a team effort to fix it," Young said. "You got folks on the floor, leadership in that area, [and] you've got engineering all working together to come up with a plan of action to create something from an idea. Then on top of it, you get this scenario where, we've essentially kind of got this project done, but we continue to keep chipping away and making it better. This is a project that started from nothing in an area where we didn't have a bunch of injuries but there was serious potential and instead of reacting to it, we were proactive. It's really a pretty classic example of an awesome project and I'm super proud of the group and all the efforts that they put into it."